Welcome to My Blog!
Before we dive into the content, I’d love for you to join me on my social media platforms where I share more insights, engage with the community, and post updates. Here’s how you can connect with me:
Facebook:https://www.facebook.com/profile.php?id=61567891941530
Now, let’s get started on our journey together. I hope you find the content here insightful, engaging, and valuable.
Caisu Machinery sells a variety of used plastic pipe production equipment. The products are of high quality and low price. Welcome to contact us for consultation and purchase. We will be happy to serve you.
Table of Contents
Introduction
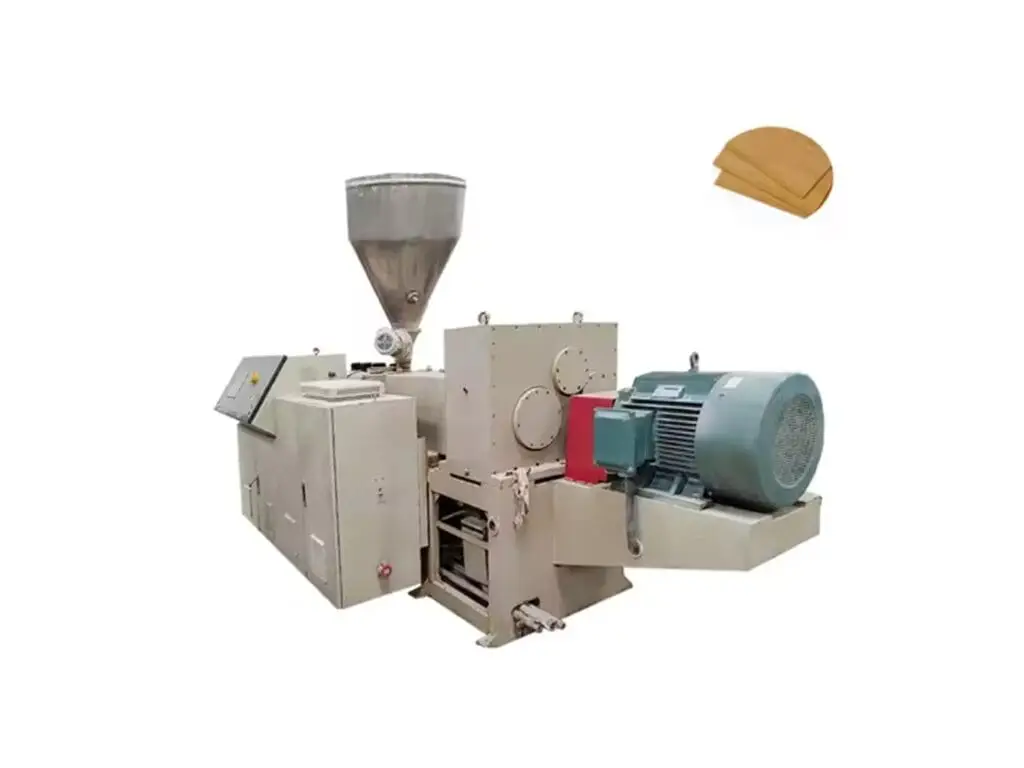
Wood-plastic composites (WPC) have gained significant popularity in various industries due to their durability, sustainability, and cost-effectiveness. A wpc extrusion machine is essential for manufacturing high-quality WPC products efficiently, combining wood fibers with thermoplastic materials to create composite materials suitable for construction, furniture, and decking applications.
Understanding the functions, features, and benefits of a wpc extrusion machine is crucial for manufacturers looking to optimize production processes and improve product quality. This article explores the key aspects of these machines, including their components, working principles, and industrial applications.
Understanding the WPC Extrusion Machine
A wpc extrusion machine is designed to mix and process wood fibers and plastic polymers, ensuring consistency and durability in the final product. The extrusion process ensures high-quality material output by precisely controlling temperature, pressure, and mixing ratios.
How a WPC Extrusion Machine Works
- Raw Material Preparation – The process begins with mixing wood powder, plastic resins (such as PVC, PE, or PP), and additives in precise proportions.
- Feeding System – The mixed raw materials are fed into the extruder, where they undergo controlled heating.
- Extrusion Process – The heated material is pushed through an extrusion screw, which ensures proper mixing and shaping.
- Shaping and Molding – The extruded material is passed through a die head, giving it the desired profile and dimensions.
- Cooling and Solidification – The shaped material is rapidly cooled to maintain structural integrity.
- Cutting and Finishing – The final product is cut, surfaced, and prepared for packaging.
Key Components of a WPC Extrusion Machine
- Extruder – The core section responsible for heating, mixing, and pushing material through the die.
- Screw and Barrel – Ensures even distribution of raw materials and consistent extrusion.
- Die Head – Shapes the material into specific profiles such as decking boards or wall panels.
- Cooling System – Uses air or water cooling to solidify the extruded material quickly.
- Cutting Unit – Provides precision in trimming the final product to the required size.
- Control Panel – Automates temperature, speed, and pressure monitoring for efficiency.
Key Features of a WPC Extrusion Machine
High Efficiency and Automation
- Utilizes advanced extrusion technology to ensure smooth and uniform production.
- Features digital control systems for precision in processing.
- Supports variable speed control for customized output.
Versatile Material Processing
- Compatible with PVC, PE, PP, and various additives.
- Enables flexibility in modifying WPC formulations for different applications.
- Supports additional surface treatments such as embossing and laminating.
Durable and Long-Lasting Construction
- Built with high-quality stainless steel to withstand long-term use.
- Includes corrosion-resistant screws and barrels for increased durability.
- Designed for 24/7 industrial operation with minimal downtime.
Energy Efficiency and Cost Savings
- Incorporates an optimized heating system to reduce power consumption.
- Ensures material efficiency by minimizing waste and maximizing output.
- Reduces overall manufacturing costs while maintaining high production capacity.
Consistent Product Quality
- Maintains precise control over raw material mixing.
- Ensures uniformity in dimensions and material composition.
- Reduces defect rates and enhances the strength of final products.
Benefits of Using a WPC Extrusion Machine
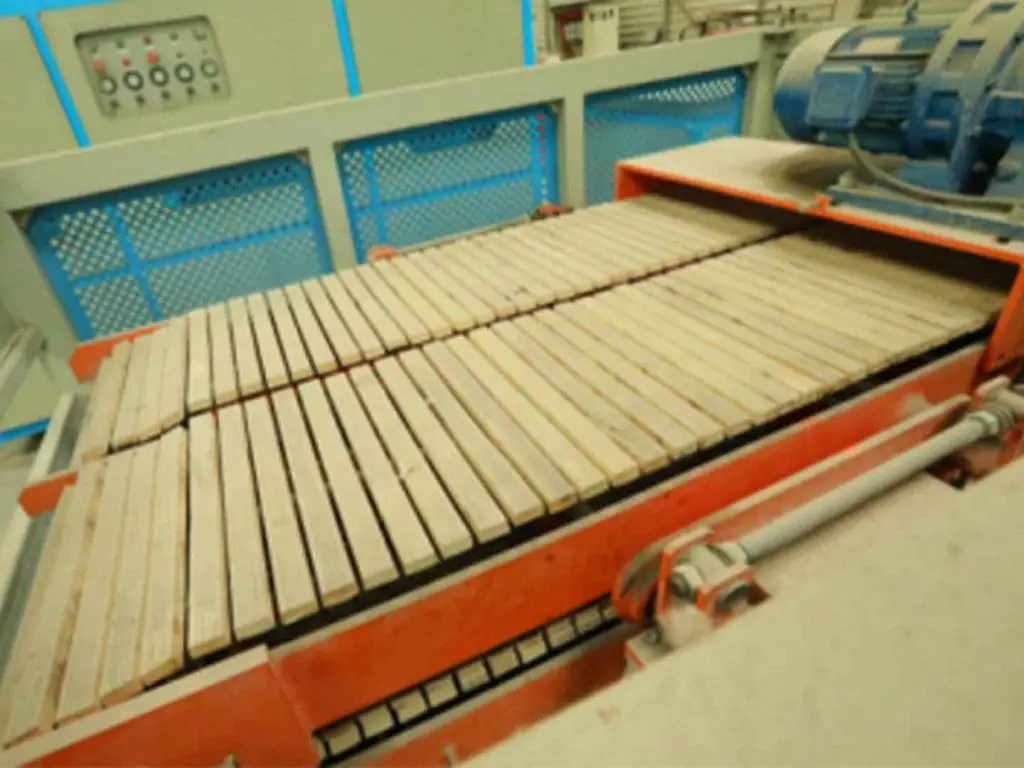
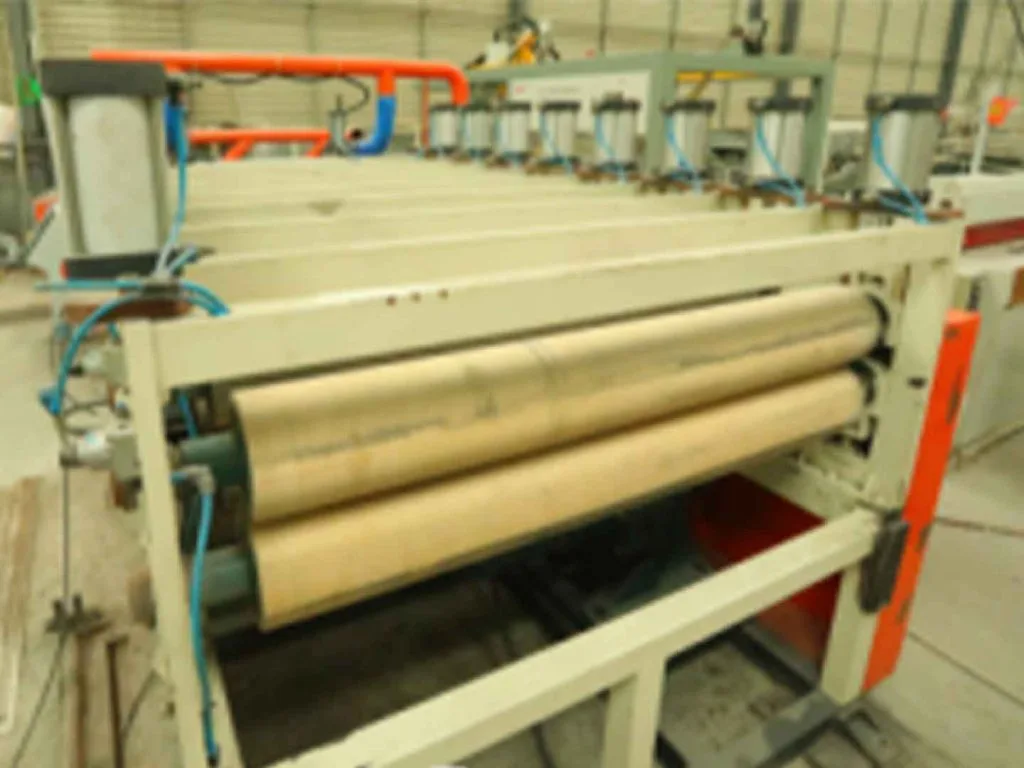
Environmentally Friendly Production
- Uses recycled plastic materials, reducing environmental waste.
- Produces sustainable WPC products that are biodegradable and reusable.
- Complies with green manufacturing standards and regulations.
Wide Range of Applications
- Ideal for manufacturing decking boards, fencing, and wall panels.
- Used in interior and exterior construction applications.
- Suitable for furniture, flooring, and outdoor structural components.
Increased Production Capacity
- Capable of high-speed extrusion to meet market demands.
- Allows for continuous, uninterrupted production cycles.
- Reduces labor costs through automation and digital monitoring.
Enhanced Strength and Durability of WPC Products
- Provides moisture-resistant and insect-resistant materials.
- Offers UV protection for long-lasting outdoor use.
- Ensures weather-resistant and fire-retardant WPC solutions.
Technical Specifications of a WPC Extrusion Machine
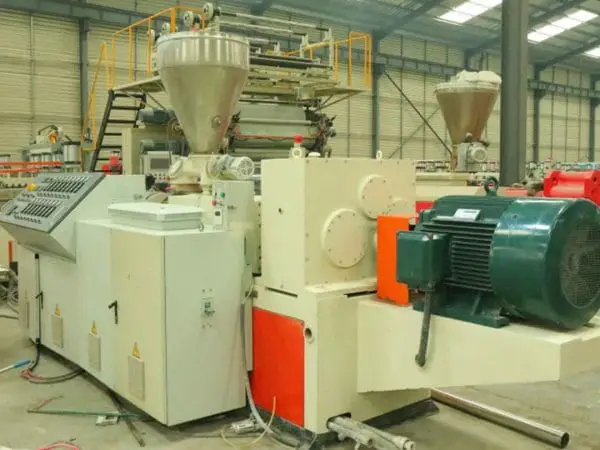
The table below highlights some essential specifications of a wpc extrusion machine:
Specification | Description |
---|---|
Extruder Type | Single-screw or twin-screw extruder |
Screw Diameter | Defines production capacity and output efficiency |
Heating Zones | Multiple heating zones for precise temperature control |
Cooling System | Water or air cooling for rapid solidification |
Die Head Design | Customizable for different profile shapes |
Material Compatibility | PVC, PE, PP, and additives |
Automation Level | Digital control system with real-time monitoring |
Production Speed | Adjustable speed control for various output requirements |
These specifications help manufacturers choose the right wpc extrusion machine based on their production needs.
Conclusion
A wpc extrusion machine is a vital asset for businesses involved in the production of wood-plastic composites. It offers high efficiency, durability, and precision, making it a reliable solution for large-scale manufacturing. With its advanced features, automated controls, and environmentally friendly processes, the machine enables manufacturers to produce top-quality WPC materials while reducing operational costs.
Understanding the technical aspects and benefits of a wpc extrusion machine ensures informed decision-making when investing in new production equipment. Choosing the right model enhances productivity, product quality, and overall business growth in the competitive WPC market.
FAQ
What is the function of a WPC extrusion machine?
A wpc extrusion machine processes wood fibers and plastic resins to create wood-plastic composite materials used in construction, furniture, and outdoor applications.
What types of products can be manufactured using a WPC extrusion machine?
Common products include decking boards, wall cladding, fencing, flooring, interior trims, and outdoor furniture components.
How do twin-screw and single-screw extruders differ?
A twin-screw extruder provides better material mixing, making it suitable for complex WPC formulations. A single-screw extruder is cost-effective and ideal for simpler production needs.
What are the key factors to consider when selecting a WPC extrusion machine?
Key considerations include extruder type, production capacity, raw material compatibility, automation level, and energy efficiency.
How can I maintain a WPC extrusion machine for optimal performance?
Regular maintenance includes cleaning the screw and barrel, monitoring temperature settings, lubricating moving parts, and inspecting the cooling system.